This work was done in collaboration with Safe Software partner IMGS.
NI Water saves 1678+ hours annually with intelligent robotic process automation and FME
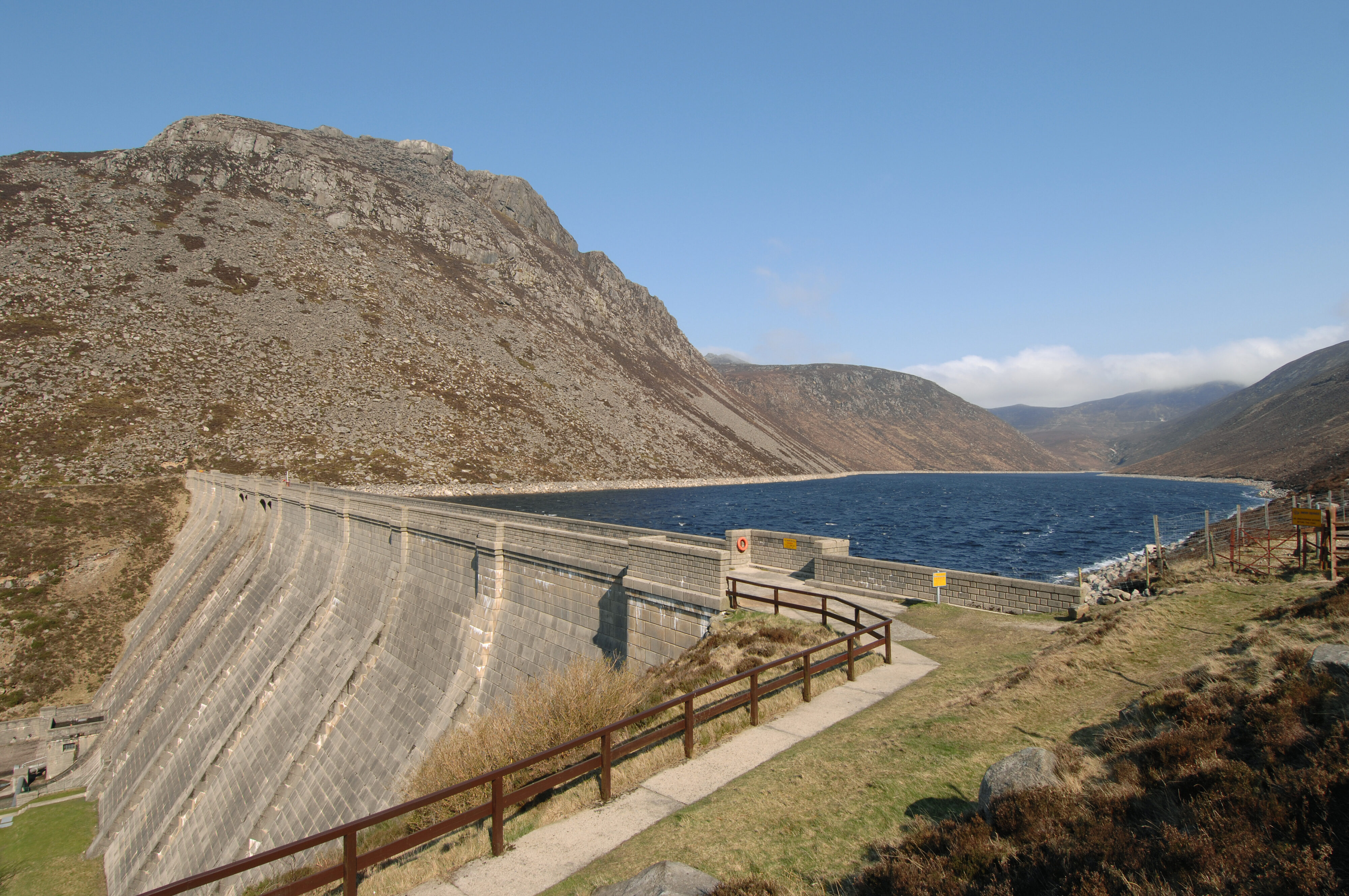
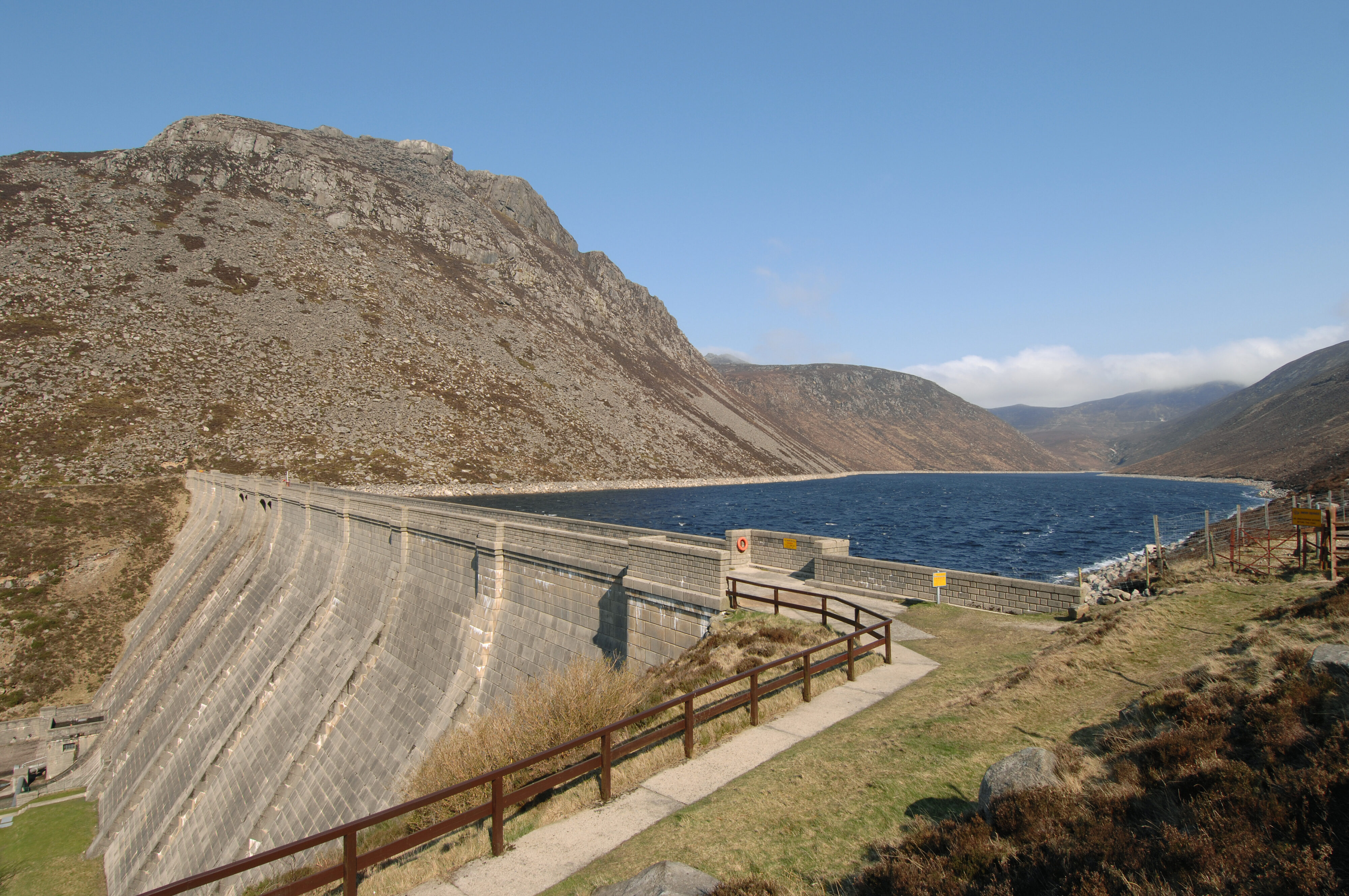
Modernizing utility workflows with AI, RPA, and FME for top-tier customer service in the UK water industry
Northern Ireland Water, a Government-Owned Company (GoCo), has been providing water and sewerage services in Northern Ireland since 2007. They deliver clean, safe, drinking water to approximately 840,000 households and businesses, providing approximately 560 million litres daily. They also collect approximately 330 million litres of wastewater daily from around 669,000 households and organizations connected to the sewerage system, overseeing safe treatment and disposal. They were also recently named the 2025 winner of the Annual Esri Ireland GIS awards in the Data Management category.
Since 2007, NI Water aimed to enhance operational efficiency through a number of projects that fully embraced asset centricity and progressively improved their technology stack. In recent years, their Planning for the Future programme proposed the funding needed to achieve their 2021-2027 targets and deliverables, centred around their key strategies and to deliver efficiencies of £32 million.
A key tenet of their goal was the establishment of a Intelligent Operations Centre, which would bring colleagues together to support enhancement of customer experience and engagement, allowing them to easily contact NI Water 24/7, and effectively utilize data to drive improvement.
NI Water set out to develop an in-house Robotic Process Automation (RPA) capability to support delivery of efficiency targets while mitigating against the absorption of work from other business areas. Candidate processes were assessed to estimate ROI and project planning, and the team quickly identified additional processes suitable for the RPA to eliminate waste and help NI Water to meet their customer engagement targets.
Completely transforming operations with automation and boosting efficiency with hundreds of hours saved yearly
The team developed a series of integral solutions:
Sewer Blockages Management
Customers submit requests, or contacts, to NI Water’s Customer Relations Centre regarding sewer blockages. Contacts require labour-intensive verification of property history to decide whether to dispatch contractors or conduct further root cause analysis (RCA). About 74% of contacts had no recent history, indicating they could be immediately dispatched to contractors. A standard work order took nearly two minutes to action, while an RCA took four minutes.
NI Water leveraged FME, using XML Templates and HTTP Callers to automate the process. Automation resulted in a success rate exceeding 99.999% and reduced average handling time to under one second, allowing the organization to handle significant workloads, including two severe weather events. FME automation established reusable tools for future projects, reducing the workload for repetitive tasks and boosting business confidence in automated systems, while also saving NI Water over 1200 hours annually.
Valving Work Orders
NI Water maintains the water distribution network through investigation, which requires manual creation of follow-up work orders for urgent valving operations work. The original process took up to 51.5 hours annually. The team implemented an automated FME process to create work orders on a schedule. The system filtered out any burst mains with related work orders and sent email notifications for situational awareness.
Since its implementation in September 2023, the system has created over 5,500 work orders, saving approximately 46 hours, equivalent to nearly six working days of manual effort.
Leakage Defect Work Orders
NI Water relied on contractors to report faults in the water network, submitting data in PDF form via email. Converting these submissions into work orders took an estimated 432 hours per year, or approximately over 52 working days.
An AI-based automation was developed, utilizing FME and Power Automate. This solution extracted data from the contractor-submitted PDFs, automatically creating work orders. The system runs efficiently in about 20 seconds per work order and saved 432 hours in FY 2023/24, allowing controllers to focus on more critical tasks.
NI Water’s use of automation, particularly using FME integrated with AI, resulted in annual time savings of over 1678 hours. The team now has faster response times, reduced manual labour, and experiences significant cost savings, while allowing their workforce to focus on value-adding activities. The success of the automation infrastructure has established reusable blocks that can be leveraged in future projects, supporting long-term growth and further digital transformation.